Task 1.1 Conductive fillers for smart mortar and smart bricks.
Task 1.1 will be a scouting and analysis of suitable conductive fillers for the novel multifunctional cement-based and lime-based mortar layers and for clay-based smart bricks, exploring in particular: MWCNT, carbon fibers, carbon black, graphene nanoplatelets, graphite, superfine micro stainless steel fibers. The most appropriate nano- and/or micro-fillers (types and producers) for conductive mortar and smart bricks will be selected considering key aspects, such as: costs, environmental issues, toxicity, mechanical properties, solubility in water and more.
Task 1.2 Dispersion of selected fillers.
Achieving a uniform dispersion of conductive fillers in cement-based, lime-based and clay-based matrices is essential to create an electrically percolating network that is responsible for the piezoresistive and damage-sensing behavior. Yet, dispersion is a difficult task, typically requiring special treatments, such as sonication, that are not suitable for large-scale productions. Task 1.2 will define appropriate fabrication and dispersion procedures, including use of physical dispersants to substitute the sonic treatment.
Task 1.3 Fabrication of smart mortar.
Task 1.3 will focus on the optimal fabrication of smart mortar considering key aspects such as type of cement or lime-based matrix, use of additives, use of specific dispersants and type of conductive filler. Fabrication procedures will be compared in terms of quality of filler dispersion. Scalable procedures will be identified for each type of conductive filler.
Task 1.4 Fabrication of smart bricks.
Various technical challenges related to smart bricks will be addressed including obtaining a composite with stable properties after burning, optimizing material, shape and position of electrodes, keeping shape and color as much similar as possible to a conventional clay brick. A collaboration with a brick manufacturing company will be established for industrializing the smart brick fabrication process.
Task 1.5 Electrical characterization.
A statistically significant number of specimens of smart mortars and smart bricks will be prepared and subjected to a variety of DC and AC electrical tests for measuring relevant properties such as resistivity and impedance, including their evolution in time and their variation with content of nano-and micro-fillers. Percolation thresholds of the different composites will be identified. The best candidate Smart Masonry enabling SAFEty-assessing STructures after earthquakes (SMS-SAFEST) composites will be selected as those exhibiting: (i) a clear percolation threshold, (ii) a significant increment of conductivity above percolation and (iii) a limited statistical dispersion of electrical properties.
Task 1.6 Strain sensing, damage sensing and mechanical characterization.
Small-sized specimens of smart mortars and smart bricks will be subjected to mechanical tests in order to assess their piezoresistive strain sensing and crack detection capabilities, as well as to address their mechanical characterization. Key strain/damage sensing parameters will be identified and their variations explored. Optimal contents of fillers will be identified for both smart mortar and smart bricks.
Task 1.7 Electronics for smart bricks.
Low-cost (e.g. based on Arduino platform) and low-impact (e.g. using recyclable materials) electronics will be designed for measuring strain using smart bricks (Figure 1).
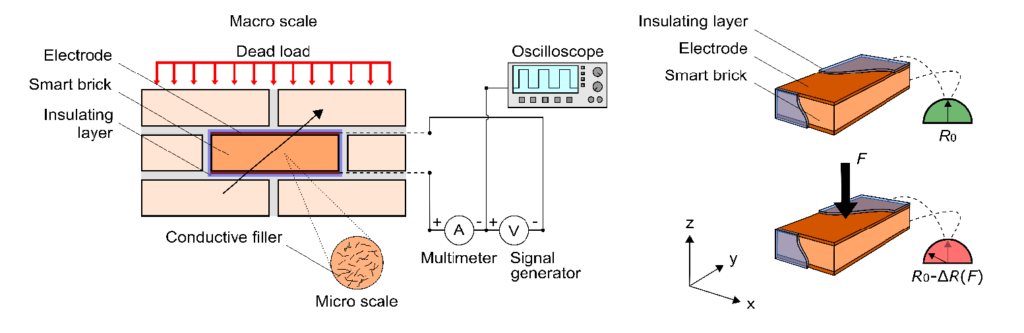
Figure 1. Deployment of a smart brick within a structural masonry element and hypothesis of measurement layout.
Bricks’ strain will be measured from changes in their electrical properties, including deployment in network configurations and using hidden wired electrodes. Signal distributors solutions will allow to obtain synchronized measurements from an arbitrary number of smart bricks with low noise and appropriate sampling rate.
Task 1.8 Electronics for smart mortar.
A multichannel, time stable, low- cost and low-impact measurement electronics for smart mortar will be developed to locally reveal a crack crossing a smart mortar layer (Figure 3). The system will be based on an array of hidden electrodes and the use of a distributed biphasic DC measurement approach.